با اتکا به توان متخصصان داخلی صورت گرفت؛
بهرهبرداری از پستهای برق ۴۰۰ و ۶۳ کیلوولت در فولاد مبارکه
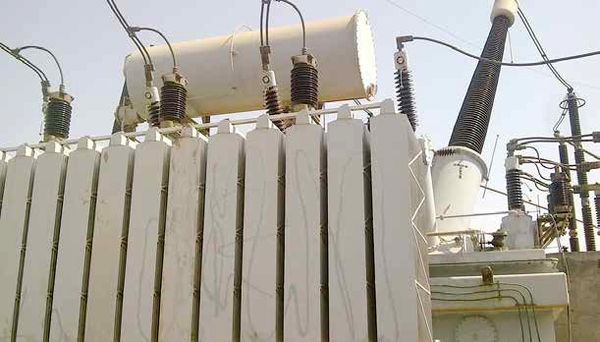
با بهرهبرداری از پروژۀ احداث پستهای برق شهید خرازی فولاد مبارکه، تغذیۀ پایدار انرژی الکتریکی سایت شهید خرازی و پایداری شبکۀ برق پیشین فولاد مبارکه از طریق تغذیۀ بخشی از بارهای آن شبکه محقق شد.
مدیر اجرای پروژههای انرژی و سیالات فولاد مبارکه ضمن اعلام این خبر و با اشاره به اهمیت اجرای این پروژه گفت: احداث پروژۀ مذکور در بهمنماه سال 1393 در زمینی به مساحت بالغبر 100 هزار مترمربع و با سرمایهگذاری بالغبر 2700 میلیارد ریال در سایت شهید خرازی شروع شد و در بازۀ زمانی چهار سال تکمیل شد و به بهرهبرداری رسید.
علیرضا استکی تصریح کرد: عمدۀ مشکلاتی که قبل از احداث این پست در شبکۀ برق فولاد مبارکه وجود داشته است عبارت بود از:
تکمیل ظرفیت حرارتی خطوط انتقال برق 400 کیلوولت فولاد مبارکه بهگونهای که هنگام تعمیر و سرویس دورهای خطوط، اعمال محدودیت برق به فولادسازی اجتنابناپذیر بود.تکمیل ظرفیت تجهیزات شبکۀ برق قبلی فولاد اعم از ترانسهای قدرت و نیروگاهها بهگونهای که با خروج از سرویس یکی از تجهیزات، بخش زیادی از مصارف خطوط تولید دچار قطعی برق و یا کاهش تولید میشدند. همچنین کاهش قابلیت اطمینان شبکۀ برق فولاد مبارکه به علت تمرکز بیشازحد بارها در پست MIS1 و بالا بودن احتمال فروپاشی شبکۀ الکتریکی و قطعی برق کامل و در نهایت عدم امکان تغذیۀ بارهای الکتریکی جدید (نظیر نورد گرم شماره 2، توسعۀ آهنسازی و...)
بومیسازی در بخش برق، علاوهبر کاهش وابستگی به سازندگان خارجی در بهرهبرداری و تعمیرات آینده، صرفهجویی سرمایهگذاری بالغبر 40 میلیارد ریال به دنبال داشته و پس از بهرهبرداری برای 75 نفر بهطورمستقیم فرصت شغلی ایجاد کرده است
مدیر اجرای پروژههای انرژی و سیالات فولاد مبارکه در خصوص مزیتهای اجرای این طرح گفت: با اجرای این پست فشار قوی، علاوهبر برطرف شدن موارد بالا، باتوجهبه اصل مهم پدافند غیرعامل در صورت بروز مشکلات فنی در شبکۀ برق قدیم شرکت از وارد آمدن هرگونه خسارت احتمالی پیشگیری خواهد شد.
وی از پست کلیدزنی 400 کیلوولت زندهرود (AIS) با هدف اتصال شبکۀ برق شهید خرازی به شبکۀ سراسری، پست مبدل 63/400 کیلوولت شهید خرازی شامل ایستگاه گازی (GIS) موسوم به NIS2 و ترانسفورماتورهای کاهنده و پست کلید زنی 63 کیلوولت شهید خرازی از نوع فضای بسته موسوم به MIS2 بهعنوان بخشهای اصلی این پست یاد کرد.
استکی با بیان اینکه کلیۀ مراحل محاسبات، طراحی، نصب، تست و راهاندازی پروژه به دست متخصصان داخلی با بیش از 730،000 نفرساعت انجام شده خاطرنشان کرد: بیش از 60 درصد تجهیزات این پست از داخل کشور تأمین شده که انتقال دانش فنی و اشتغالزایی قابلتوجهی به همراه داشته است.
وی افزود: مراحل راهاندازی و بهرهبرداری از پروژه به این شرح بوده است: برقداری پست کلیدزنی 400 کیلوولت زندهرود؛ برقداری پست گازی 400 کیلوولت شهید خرازی؛ برقداری ترانسفورماتورهای کاهنده و پست کلیدزنی 63 کیلوولت شهید خرازی و انتقال تغذیه برق مگامدولهای احیامستقیم شهید خرازی به پست جدید.
تشریح وضعیت فعلی این پروژه بخش دیگری از سخنان استکی بود. وی در این خصوص گفت: در حال حاضر، تغذیۀ برق مگامدولهای احیا مستقیم شهید خرازی که قبلا بهصورت موقت از پست MIS1 برقرار بوده به پست MIS2 منتقل شده و حدود 40 مگاوات از بار شبکۀ برق قدیمی فولاد مبارکه کاسته شده است. همچنین بارهای واحدهای گندلهسازی و مدولهای احیا مستقیم نیز در آینده به پست جدید منتقل خواهد شد و تغذیۀ برق نورد گرم شماره 2 نیز در آینده از محل پست جدید پیشبینی گردیده است. در حال حاضر ظرفیت نصبشدۀ تجهیزات در این پروژه 500 مگاولت آمپر است که تا 1500 مگا ولتآمپر قابلیت توسعه دارد.
با بهرهبرداری از پروژۀ احداث پستهای برق شهید خرازی فولاد مبارکه، تغذیۀ پایدار انرژی الکتریکی سایت شهید خرازی و پایداری شبکۀ برق پیشین فولاد مبارکه از طریق تغذیۀ بخشی از بارهای آن شبکه محقق شد
وی در ادامه از این طرح بهعنوان یکی از موفقترین پروژههای اجراشده در فولاد مبارکه نام برد و اظهار داشت: بهمنظور استفادۀ حداکثری از توان تولید داخلی، برخی از تجهیزات پروژه بهرغم داشتن امکان تأمین خارجی پیشبینی شده در قرارداد، بومیسازی شدند که مهمترین آنها عبارتند از: سیستم ثبت خطاها و وقایع (Fault & Event Recorder) پست MIS2؛ تغییر سازنده از زیمنس آلمان به بهینه نیرو؛ راکتورهای سری 6/6 کیلوولت؛ تغییر سازنده از ترنچ اتریش به فراپیام؛ تابلوی میمیک موزاییکی؛ تغییر سازنده از دوموی ایتالیا به طرح نیرو.
استکی در همین خصوص افزود: بومیسازی موارد فوق، علاوهبر کاهش وابستگی به سازندگان خارجی در بهرهبرداری و تعمیرات آینده، صرفهجویی سرمایهگذاری بالغبر 40 میلیارد ریال به دنبال داشته و پس از بهرهبرداری برای 75 نفر بهطورمستقیم فرصت شغلی ایجاد کرده است.
ساخت اولین ضخامتسنج گامای خاورمیانه در شرکت فولاد مبارکه
اولین ضخامتسنج گامای محصولات گرم فولادی کشور با تکیه بر دانش فنی متخصصان داخلی شرکت فولاد مبارکه با موفقیت بومیسازی شد.
کارشناس تعمیرات سیستمهای اندازهگیری نورد گرم ضمن اعلام این خبر افزود: تولید محصول مطابق با استانداردهای بینالمللی و تأمین درخواست مشتری، به خطوط تولید مدرن و تجهیزات دقیق اندازهگیری نیاز دارد؛ به همین منظور در خطوط نورد گرم، دستگاههای ضخامتسنج از جایگاه ویژهای برخوردارند.
وی با بیان اینکه در خروجی نورد نهایی یک ضخامتسنج گامای ساخت شرکت توشیبای ژاپن قرار داشت افزود: قسمت محاسبات این تجهیز به دلیل استهلاک و آنالوگ بودن در سال 1391 از مدار بهرهبرداری خارج شد.
حسن اصغریپور در تشریح روند ساخت این تجهیز افزود: پس از تهیه نقشۀ C-Frame، ساخت آن در دستور کار تعمیرگاه مرکزی قرار گرفت. در ادامه قطعات موردنیاز از داخل کشور تهیه و مونتاژ شد. پس از آن تابلوی کنترل تهیه و در سالن برق نصب گردید و کابلهای موقت تا C-Frame کشیده شد. در همین راستا با توجه به استراتژیک بودن PC-Base کامپیوتر سرور و نرمافزارهای موردنیاز تهیه شد. وی خاطرنشان کرد: پس از اقدامات فوق، اندازهگیری ضخامت با سورس گاما و آشکارساز Ion-Chamber آغاز شد که با بروز مشکلات بعدی، تصمیم بر آن شد که از آشکارساز Scintillator استفاده شود. پس از نصب آشکارساز لازم بود سیگنال آنالوگ خروجی به دیجیتال تبدیل شود تا در سیستم کنترلی که بر پایۀ PC طراحی شده بود قابلاستفاده باشد. در ادامه، برطرف کردن مشکلات تقویتکنندۀ نوری که نیاز به ولتاژ بالا داشت در دستور کار قرار گرفت.
پس از آمادهسازی این مراحل، نوبت به انتخاب روش اندازهگیری ضخامت شد. نظر به تجربیات و مستندات مربوط به ضخامتسنجهای موجود، روش اندازهگیری «میزان تضعیف» برای ضخامتسنجی انتخاب و برنامۀ مربوط به آن نوشته شد. در نهایت پس از انجام آزمایشهای لازم به صورت سرد و اطمینان از عملکرد صحیح آن، تجهیز به خط منتقل شد و اتصالات موردنیاز آن مثل آب خنککاری، کابلهای برق و شبکه برقرار گردید و تجهیز با حمایت جدی و قبول خطرات مرتبط، توسط مدیریت ناحیه و همکاری سایر بخشها، تست گرم را با موفقیت پشت سر گذاشت و خوشبختانه نتایج اندازهگیریها در مقایسه با ضخامتسنجهای دیگر رضایتبخش بود و عملکرد بسیار خوب تجهیز را نشان میداد.
اصغریپور با تأکید بر اینکه در این پروژۀ بزرگ علاوهبر رفع مشکلات ناشی از توقف تجهیز و خط تولید، از خروج حدود 240 هزار یورو برای خرید هر تجهیز جلوگیری و دانش فنی ساخت این تجهیز نیز بومیسازی شد، گفت: این موفقیت با همکاری و همدلی همکاران گرامی از تعمیرات سیستمهای اندازهگیری نورد گرم، کنترل پروسس، تعمیرگاه مرکزی، آزمایشگاه پرتوزا و الکترونیک و حمایتهای مدیریت ناحیه به دست آمد که از همۀ این عزیزان قدردانی میکنیم.
در همین خصوص امیر گودرزی، رئیس کنترل فرآیند نورد گرم افزود: انجام این فعالیتهای مهندسی و نوآورانه در واحد از آن جهت باارزش است که در زمانی که با محدودیت در انتقال دانش فنی و تجهیزات مواجهیم، میتوانیم با استفاده از هوش و استعداد ذاتی و فعالیتهای همکاران بر بسیاری از مشکلات پیش رو غلبه کنیم.
علی حاجیاننژاد، مدیر ناحیۀ نورد گرم نیز ضمن تبریک این موفقیت گفت: محدودیتهای سالهای اخیر نهتنها باعث توقف کار و تولید در فولاد مبارکه نشد، بلکه شرایطی فراهم کرد که کارکنان با اتکا به دانش فنی بومی بسیاری از تجهیزات را بومیسازی کنند و بومیسازی ضخامتسنج مذکور که ممکن بود به موضوعی بحرانی مبدل گردد، خوشبختانه با اتکا به دانش فنی و تجربه تیمی بعد از چندین ماه تلاش بیوقفه این اراده و تصمیم به نتیجه رسید و این ضخامتسنج با موفقیت کامل در مدار بهرهبرداری قرار گرفت. کسب این موفقیت بزرگ را به همۀ کارکنان فولاد مبارکه و مخصوصا تیم مهندسی و متخصص نورد گرم تبریک میگوییم.
رشد 11 درصدی تولید محصولات نورد سرد
با همت کارکنان سختکوش ناحیۀ نورد سرد در دوماهۀ اول سال «رونق تولید»، میزان تولید محصولات سرد در این ناحیه با 11 درصد رشد در دوماهه اول سال جاری به 274 هزار تن رسید.
مدیر ناحیۀ نورد سرد ضمن اعلام این خبر گفت: محصولات پوششدار بهطورمتوسط 4 درصد رشد داشته و تولید آن به 70 هزار تن طی دوماهۀ ابتدایی سال جاری رسیده است. ضمن اینکه میزان تولید محصول قلعاندود به رشد قابلتوجه 9 درصد رسیده است.
سید مهدی نقوی از کاهش توقفات خطوط ناحیۀ نورد، افزایش تن بر ساعت تولید، بهبود برنامهریزی تولید و حمل محصول بهعنوان مهمترین دلایل کسب این رکورد یاد کرد.
وی افـزود: باتوجه به اختلاف قیمت محصولات داخلی و مشابه خارجی و عزم کشور برای کاهش واردات محصولات سرد و جلوگیری از خروج ارز، تولید حداکثری محصولات کیفی در سال 98 بهمنظور تأمین نیاز مشتریان پاییندست در دستور کار ناحیۀ نورد سرد فولاد مبارکه قرار گرفت.
مدیر ناحیۀ نورد سرد از صنایع خودروسازی، تولیدکنندگان لوازم خانگی، فیلترسازان، بشکهسازان و سایر صنایع پاییندستی بهعنوان مشتریان عمدۀ ناحیۀ نورد سرد نام برد و گفت: برنامهریزی برای تداوم و بهبود هرچه بیشتر ظرفیت تولید در این ناحیه در حال انجام است.
دیدگاه تان را بنویسید